高まる品質要求、設備・機械にも工夫(マレーシア)
進出日系メーカーの品質管理事例(1)
2018年6月22日
ASEANで操業する日系企業が抱える経営課題はさまざまだが、多くの企業が共通して頭を悩ますのは品質の維持および向上だ。「品質管理の難しさ」は在マレーシア日系企業へのアンケートで、最も多く挙げられる経営課題だ。マレーシアにおける進出日系メーカーの品質管理の取り組みと課題を2回に分けて紹介する。
「品質管理」が最大の経営課題
ジェトロが2017年10~11月に実施した「2017年度アジア・オセアニア進出日系企業活動調査(ジェトロ調査)」によると、ASEAN(ブルネイを除く)における進出日系企業の経営課題の上位項目は「従業員の賃金上昇」「品質管理の難しさ」「原材料・部品の現地調達の難しさ」「従業員の質」「競合相手の台頭(コスト面で競合)」が占めた。
ASEANの中でも製造業の進出日系企業が多い主要5カ国(マレーシア、タイ、インドネシア、フィリピン、ベトナム)でこれら5項目の回答企業の割合をみると、マレーシアは「品質管理の難しさ」でASEAN平均値および他国と比較して10ポイント以上高い(図1参照)。
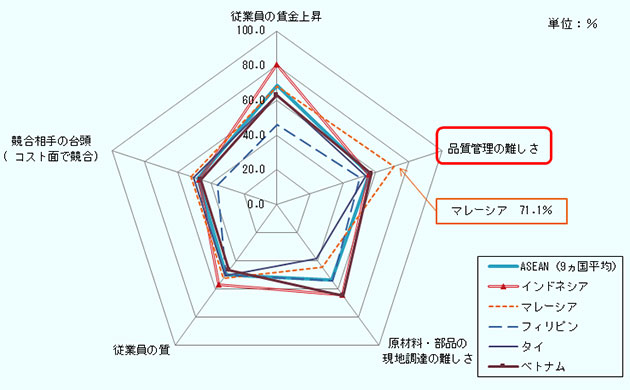
- 出所:
- 2017年度「在アジア・オセアニア進出日系企業実態調査」
在マレーシア日系企業が抱える「品質管理の難しさ」について具体的にみると、「検査要員の人為的ミス(見逃し)が多い」(79.5%)、「作業者の品質意識が低い」(68.5%)に、「機械化が難しい」(30.1%)、「熟練工の定着率が低い」(28.8%)が続く。多くが従業員に関する課題である。
在マレーシア日系製造業の約4割が「電気・電子製品および部品」、1割強が「輸送機械・部品」や「一般機械・部品」の生産に携わる。マレーシアでは近年、国内自動車産業向けの車載用電子部品や航空機部品など高付加価値製品の需要が高まりつつある。こうした製品は他産業と比べて高い品質を求められる。最近、車載用電子部品の注文が増えたという日系メーカーは「車載用部品は一般の電子部品と比べ品質要求が10倍ほど高い」という。
材料調達先の管理が品質の要
品質管理の手法は多岐にわたるが、在マレーシア日系製造業による品質管理の取り組みと課題について、品質管理の要素である5Mに沿って概観する。5Mとは、(1)材料(Material)、(2)機械(Machine)、(3)人(Man)、(4)方法(Method)、(5)測定・検査(Measurement)を指す(図2参照)。
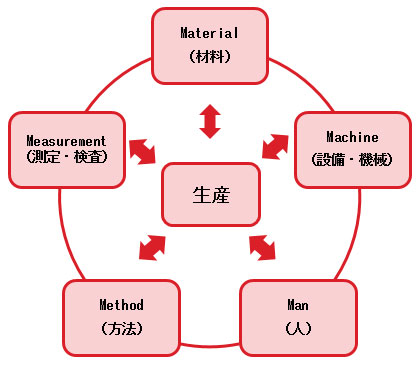
- 出所:
- 日本科学技術連盟の資料を基にジェトロ作成
まず、1つ目のMである「材料」について。原材料・部品の調達は、製品の製造コストや品質に密接に関わる要素だ。コストや納期の面から現地調達が最も経済的だが、品質面から現地で調達できない材料・部品も多い。2017年度のジェトロ調査によると、在マレーシア日系製造業は約4割を現地調達し、残り6割は海外から調達している(平均値、金額ベース)。
材料・部品のばらつきを管理するための施策としては、(a)供給元の指定、(b)供給元への指導、(c)調達した材料・部品の検査などが行われている。(a)では、品質の要となる基幹部品を日本から輸入するという企業が多い。2016年度のジェトロ調査によると、「日本でしか調達できない原材料・部品の有無」について、在マレーシア日系製造業の80.9%が「ある」と回答しており、その最大の理由として「品質・技術面の理由から日本でしか生産できない」(83.5%)が挙がった。
電子機器メーカーA社の現地調達率は7~8割と、在マレーシア日系企業の平均値の2倍近い。A社工場に隣接する地場工場では、A社へ納入する関連部品の生産が行われており、A社工場には、不良品が搬送された際に対処する専門スタッフが常駐している。また、A社では特に品質のばらつきが多いサプライヤーからの納入部品は全量検査を行うことでリスクを最小限に抑えている。とはいえA社でも、電子部品を中心に基幹部品などは日本からの調達に依存している。A社以外の他メーカーでも、基幹部品については高い品質要求を満たすため、日本から輸入している企業が多いようだ。
機械の稼働状況をリアルタイムで確認
2つ目のMは「設備・機械」だ。製造に使用する機械の不具合は、品質のばらつきに直結する。日系メーカーでは、電子あんどんやIoT(モノのインターネット)を活用して機械の稼働状況をリアルタイムで監視し、不具合や故障に即時対応している。
機械メーカーB社では、工場内に設置する全ての機械にデータ収集装置を取り付け、収集したデータを工場内の一角にあるデータセンターで一元管理できる仕組みを取り入れている。機械が故障し、修理をする場合、どのような故障で、誰が、どれくらいの時間をかけて対応したか、故障は完全に直ったかなどといったデータを常に記録し、工場内で共有している。こうしたデータ収集の積み重ねが、故障が多い機械や工程の見直しや改善に役立っている。データ収集、分析に使用するソフトウエアの開発は、工場近くの中小システムベンダーに委託している。B社によると「開発コストが安く、投資回収期間が1~2年と短くて済む」という。
電子部品メーカーのC社は、「ローカルの作業員は、機械にわずかな不具合があっても、そのまま作業を続けてしまう傾向にある」と指摘する。C社では、少しでも不具合が生じた場合には生産ラインを即時停止し、問題が解決するまで稼働しないというルールを徹底している。機械の不具合が品質に影響するという意識を現場に浸透させることも有効な対策だ。

- 執筆者紹介
-
ジェトロ・クアラルンプール事務所
田中 麻理(たなか まり) - 2010年、ジェトロ入構。海外市場開拓部海外市場開拓課/生活文化産業部生活文化産業企画課/生活文化・サービス産業部生活文化産業企画課(当時)(2010~2014年)、ジェトロ・ダッカ事務所(実務研修生)(2014~2015年)、海外調査部アジア大洋州課(2015~2017年)を経て、2017年9月より現職。